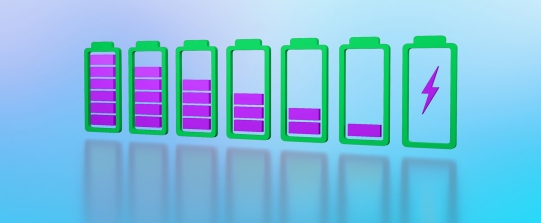
DOWNLOAD
DATE
Contact
Electric vehicles (EVs) have seen remarkable growth, especially in the automotive and public transportation sectors. However, their up-front cost hampers further expansion. Addressing this challenge involves reducing the most substantial fixed cost element: the battery. This Viewpoint explores the practice of repurposing as an option for reducing costs. Despite great potential, the market for repurposing is still evolving, presenting both challenges and opportunities.
While recycling is a common practice for used EV batteries, repurposing has emerged as a potentially more beneficial option, generating additional revenue, reducing waste management costs, and contributing to lowering the total cost of manufacturing and operating EVs.
Batteries in EVs can have a remarkably long lifespan. However, once they reach 70%-80% of their original capacity (a battery’s state of health [SOH]), they are deemed nonviable in the vehicle. Repurposing involves processes like collection, discharge, assessment, disassembly, and reconfiguration of a battery into a new application. This taps into the remaining useful life of the battery, generating additional revenue and increasing its overall economic value.
While current practices involve shipping batteries to recycling plants once removed from a vehicle, the evolving landscape, including new battery chemistries — lithium iron phosphate (LFP) versus nickel manganese cobalt (NMC) — and changing regulations, suggests a potential shift. Investors are now allocating capital toward both recycling and emerging second-life opportunities. Second-life batteries (SLBs) find applications in stationary systems, combined with renewable energy sources, grid support, and behind-the-meter-electricity storage for residential, commercial, and industrial properties. Figure 1 shows the lifecycle of a vehicle battery, including possible recycling and repurposing processes and second-life applications.
THE GROWTH OF EVs
In 2022, EVs achieved a historic milestone, accounting for over 10% of global vehicle sales. China led other regions, with EVs representing 19% of all sales, followed by Europe with 11%. Beyond being a step toward a more sustainable future, these figures indicate a tipping point in mass EV adoption. As more EVs approach the end of their lifecycle, attention shifts to handling the batteries of retired vehicles. By 2030, we expect more than 17 GWh of EV batteries to become available for repurposing from cars, buses, vans, and trucks, as shown in Figure 2.
Battery costs still constitute close to 40% of total EV costs across the industry, a significant factor in EV manufacturing. With lithium-ion (Li-ion) battery technology continuing to dominate, global raw material prices have surged over the last three years. Lithium commodity prices have increased over 1,000% since 2020, resulting in a notable uptick in Li-ion battery pack prices. Prices for other raw materials used in battery manufacturing have also surged in the recent past (see Figure 3). This has been caused by the expanding demand for EVs coupled with the inelastic nature of the mining industries (i.e., limited ability of supply expanding when prices increase). Reusing batteries becomes attractive as a means of price hedging and ensuring a reliable supply for energy storage providers, especially with the rise of lower-value chemistries like LFP.
Battery types
As illustrated in Figure 4, there are five main Li-ion battery cathode chemistries: (1) NMC (and NMCA, a variation containing aluminum), (2) NCA (nickel cobalt aluminum oxide), (3) NMA (nickel cobalt manganese aluminum oxide), (4) LCO (nickel- and/or cobalt-heavy), and (5) LFP (iron- and phosphate-based). While NMCs dominate today’s EV market, LFPs gain traction in personal EVs, electric buses, and trucks. The traditional route has been to recycle those materials to recapture the most value from the battery. However, the less valuable materials in LFP batteries (consisting mainly of iron and phosphate) raise concerns about the economic feasibility of recycling, making second-life applications an appealing alternative.
SLBs AS VALUE-ADDING SOLUTION
Historically, battery-recycling capacity in the US and the EU has been limited, with two-thirds of the recycling capacity located in East Asia at the end of 2021. Most used batteries were shipped to these facilities to be recycled. More recently, given that recycling is increasingly recognized as a key economic activity and regulations favor it, a variety of players interested in tackling Li-ion battery recycling have emerged worldwide. These include tech-focused start-ups, chemical and waste management companies, as well as battery and automotive manufacturers striving for an integrated approach. Examples of new facilities include Redwood Materials’s recycling plant in Reno, Nevada, USA, and Umicore’s facility in Hoboken, Belgium. Although specific techniques may differ, the concept of recycling EV batteries remains consistent across major players, such as Redwood Materials and Li-Cycle in North America and Glencore and Umicore in Europe. Multiple collaborations are forming with players aiming to establish the right partnerships to cover several steps of the battery-recycling value chain.
The appeal of recycling to these companies lies in extracting valuable materials from used batteries that can then be utilized in new products, including vehicle batteries, creating an element of a circular economy in the EV sector. This presents a potentially profitable business case, contingent on the value of recovered materials and the disposal fees paid by original equipment manufacturers (OEMs). However, it falls short in capturing the value from any potential remaining useful life within the original batteries.
In contrast, repurposing captures the value of end-of-life EV batteries by reconfiguring used batteries into a useful electricity-storage product. This not only generates more revenue but also reduces costs for battery owners (e.g., vehicle OEMs). Additional revenue streams can be established by selling used batteries to a “repurposer” (e.g., energy storage companies) or selling repurposed products (e.g., industrial storage solutions) directly to end users. The former can be achieved through a longer-term partnership with a repurposer. Consequently, the initial cost of battery manufacturing can be spread over an extended period of revenue generation. In this way, second-life applications contribute to the reduction of waste management costs for OEMs.
To retain ownership of batteries, maximize profitability, and reduce the overall cost to the consumer, OEMs are implementing battery-leasing programs. These initiatives separate the battery from the vehicle’s sale, resulting in a more affordable vehicle for the customer, while OEMs retain ownership of the batteries. This approach gives OEMs the flexibility to become repurposers and/or asset operators themselves or enter partnerships with energy specialists. In doing so, they diversify their business portfolios into clean energy, earning a premium on their valuation multiple compared to their peers.
MOVE TOWARD INTEGRATED BATTERY ECOSYSTEM
The SLB supply chain is in its nascent stages. The EU’s new battery regulation aims to structure the ecosystem by assigning responsibilities to battery producers for end-of-life treatment. By 2026, repurposing is expected to become less costly, supported by the EU’s requirement of battery passports for industrial and EV batteries.
For example, UK-based Connected Energy has taken an early leadership position by forming partnerships across the value chain despite market ambiguity (see Figure 5). The company connects individual, unchanged battery packs from OEMs and operates them as part of a battery energy storage system (BESS) unit and has introduced several related pilot projects. The approach aims to overcome market ambiguity by providing a missing link between the original battery owners (OEMs) and second-life users (i.e., utilities, commercial and industrial [C&I] companies, and residential storage providers).
Similar ecosystems are emerging globally:
-
In Japan, Nissan and Sumitomo Corporation formed a joint venture to develop an ecosystem for recycling, reselling, and reusing Nissan EV batteries.
-
China, through its Ministry of Industry and Information Technology, is addressing second-life safety concerns, with companies like BYD capitalizing on the anticipated increase in returning EV battery feedstock.
-
The EU battery regulation and policies promote circularity in the battery value chain, with pilot projects involving OEMs and utilities. Enel X, for instance, participates in notable SLB initiatives, including collaborations with Nissan in Melilla (maximum stored energy capacity of 1.7 megawatt hours [MWh]) and at Rome-Fiumicino International Airport (in partnership with three OEMs, with a 10 MWh capacity, and partially funded by a grant of €3.15 million [US $3.4 million] from the EU Innovation Fund).
-
In Germany, Mercedes-Benz deployed second-life BESSs in Hanover (17 MWh) and Lünen (13 MWh) in 2023, in partnership with utility Enercity AG and vehicle-to-grid specialist The Mobility House, respectively.
-
In the US, despite a lack of dedicated policy, several start-ups are developing proprietary technologies for second-life diagnostics, extraction, and integration. This includes B2U Storage Solutions (which expanded its in-house BESS in Lancaster, California — used in the CAISO wholesale power market with over $1 million in revenue — to 25 MWh), as well as Smartville, and RePurpose Energy.
CHALLENGES TO NAVIGATE IN A NEW MARKET
As the feedstock of used EV batteries grows and the market becomes more defined, the value proposition of SLBs becomes more attractive. However, navigating current challenges is crucial for success in this emerging market. For those looking to capitalize on the emerging repurposing ecosystem, it is important to formulate an effective strategy to enter this market.
Economic challenges
Figure 6 highlights the economic challenge of repurposing to compete with recycling. The high value of NMC raw materials — cobalt, manganese, and nickel — has made it challenging for repurposing to viably compete with today’s recyclers such as Umicore and Li-Cycle. Achieving profitability requires a focus on battery passport implementation and technology innovation for process automation. Ambiguity in the value chain poses scalability challenges, but major players are addressing this through in-house circular value chain solutions and partnerships. For LFP batteries, recycling is usually not commercially attractive, as the raw materials are less valuable.
Repurposing has so far only been tested at the pilot level, and partnerships between OEMs, transporters, repurposers, and end customers are not truly defined, posing scalability challenges. Nevertheless, companies like Mercedes, Volvo, Volkswagen, and BMW are addressing these issues by testing in-house circular value chain solutions in collaboration with SLB ESS providers. Prominent European utilities like RWE, Engie, and Enel are piloting SLB ESS projects and investing in start-ups, positioning themselves advantageously for the future.
Technical challenges
Predicting the life expectancy of SLBs is challenging. Due to the limited use cases to test the degradation of SLBs, estimations for SLB life expectancy must be performed through simulations. Unlike first-life battery-degradation rates that are predicted based on empirical testing, SLB estimations are a relatively riskier alternative. However, electric fleet vehicles are highly monitored (e.g., driving pattern and storage), making the SOH of used EV fleet batteries much easier to predict than that of a passenger vehicle (PV). PVs will drive wider ranges of routes, charge with various voltages, and experience different temperatures — all resulting in higher uncertainty in the SOH for SLBs. However, battery-performance estimation start-ups such as TWAICE and Recurrent, and the EU’s introduction of battery passports, are creating business opportunities that could eventually solve these challenges.
Conclusion
TAPPING THE SLB MARKET
As the EV market evolves, an ecosystem for SLBs has emerged as an option to generate additional revenue, reduce waste, and lower costs of manufacturing and operation. Opportunities exist across the sector:
-
Energy companies and investors: take a broad view of the EV market. As used EV battery volumes grow and LFP chemistry gains market share, industry collaboration and policy actions play a crucial role in supporting SLB growth. LFP chemistry is expected to increase market share, and new EV segments are expected to grow and contribute to available feedstock. Choose multiple suppliers to reduce dependence on regional feedstocks.
-
Storage developers and utilities: run pilot projects. SLBs offer a solution to reduce total cost of ownership and create new revenue streams by extending battery lifespan under specific market conditions, including innovation in ecosystem (e.g., battery passport) and technology (e.g., battery monitoring, testing), battery price increase (e.g., due to supply-demand imbalance), and low-value chemistries with LFP. Pilot projects allow companies to gain experience and understanding of the market and industry.
-
All market participants: seek partnerships with players along the value chain. The SLB ecosystem is not fully developed, providing opportunities for innovators and fast movers. Strategic entry into the market is required through pilots and strong partnerships between different players along the value chain, including independent automotive OEMs and small and medium-size enterprises active along the supply chain as well as global multi-utilities.