12 min read • Automotive, Sustainability, Technology & innovation management
Opening the urban mine
Building a profitable circular economy based on a lithium battery recycling example

Creating circular supply chains is essential to the green transition, particularly when it comes to recycling and reusing rare materials. Yet, while many circular economy initiatives may be sustainable, they are not profitable, which hampers their wider development and holds back the achievement of sustainability goals.
Lithium-ion (Li-ion) batteries are a key case in point. Powering electric vehicles (EVs) and renewable energy storage are central to decarbonization and the green transition. According to Arthur D. Little (ADL) forecasts, after surpassing the 1 terawatt hour (TWh) threshold in 2023, global annual Li-ion battery demand will increase to roughly 5 TWh by 2030 and 7 TWh by 2035. However, battery production relies on large amounts of metals (e.g., lithium, manganese, cobalt, and nickel) that generate significant ESG (environmental, social, and governance) risks and carbon footprints when mined, processed, and manufactured. The EU Commission estimates that the global demand for active battery materials such as lithium, graphite, and nickel will double between 2025 and 2030 (see Figure 1). The decade after 2030 will see a further dramatic increase in material demand. However, since the lifetime of batteries in EVs and stationary storage can exceed 10 years easily, the availability of spent batteries for recycling will remain limited during the next decade. For example, in Europe, the material will hardly surpass 1 million metric tons before 2035.[1]
Recycling end-of-life (EOL) Li-ion batteries (from laptops, consumer electronics, and, mainly, an increasing number of EVs) and reusing their components in new batteries should present a clear opportunity to marry sustainability and profitability. The EU Commission expects about half of the demand for nickel and cobalt for batteries in 2040 to be covered by output from recycling facilities.[2] However, in many regions, battery recycling business models are not profitable because of the need for high-CAPEX investments, low current volumes, immature technology, volatile raw material prices, and difficulties in scaling. Over three-quarters (77%) of experts in our analysis agree that recycling EOL Li-ion batteries in Europe is currently not economically viable.
This leads to the unsustainable practice of exporting black mass (partly processed EOL battery materials) to Asia, adding to transport emissions and impacting access to rare minerals required by the growing European battery industry. Global markets reflect this with lower prices for black mass in Europe due to lower local processing capacity, and thus demand, as well as the costs of shipping to Asia.
How can an economically viable circular model be put in place? Based on ADL research of industry players and our experience within client projects, this article sets out a blueprint for urban mining to successfully and profitably recycle Li-ion batteries locally. This template not only helps create a circular economy around batteries but provides best practices that can be applied to other recycling initiatives, such as electronics, plastics, and metals.
BUILDING A CIRCULAR ECONOMY AROUND BATTERIES
The growth of EVs focuses attention on the importance of Li-ion battery production to national and regional economic competitiveness. This leads to an increase in regulations designed to secure supplies of specific materials while governments encourage the creation of battery gigafactories through subsidies and incentives.
THE GLOBAL REGULATORY PICTURE
Regulations around battery recycling and sourcing rare materials vary worldwide but show an overall trend toward stricter standards. Asia, especially South Korea and China, was a notable first mover, with battery recycling regulations in place since 2013. This led to a current recycling rate of approximately 90% and a well-developed, profitable circular economy around batteries.
The EU’s 2006 Battery Directive set a 55% recycling rate target. Realizing this was insufficient, its 2023 Battery Regulation marks a shift toward establishing a closed-loop battery value chain. This includes targets for both recycling particular materials and their reuse in the production of new batteries, including:
- Increasing lithium recycling rates from 50% to 80% between 2028 and 2032
- Increasing cobalt, copper, nickel, and lead recycling rates to 90% from 2028, rising to 95% by 2032
In the US, there is no overarching requirement for battery recycling. However, initiatives such as the Department of Energy’s Lithium-Ion Recycling Prize and programs such as Call2Recycle actively promote and improve battery recycling practices. Furthermore, the Critical Minerals and Materials (CMM) Program indirectly encourages battery recycling by listing certain materials, including cobalt and nickel, as essential for clean technology.
CURRENT CIRCULAR ECONOMY BUSINESS MODELS
Batteries for recycling come from two sources: production scrap from battery gigafactories and EOL batteries from EVs, energy storage, cellphones, and laptops. The average life of EV batteries in first and (less demanding) stationary second-life applications is estimated to reach 10-15 years easily. That means most recyclers focus on batteries from production scrap, especially through closed partnerships between battery manufacturers and recyclers.
This will change in the medium term as EV numbers increase. In Europe, 2030–2035 is forecast to be the cross-over point when EOL volumes from EVs overtake production scrap to form the majority of recycling stock. This will enable new business models, such as vehicle OEMs or battery manufacturers, to retain ownership of the battery materials and use recycling companies as service providers to carry out the extraction process.
In Asia, where battery and EV production picked up earlier, recyclers have already built and begun operating large-scale hydrometallurgy facilities, processing black mass, including from Europe, at scale. This enables more economical operations and has stimulated a strong local market for black mass, resulting in prices around 20% higher than in Europe. The combination of these higher prices and a dearth of current hydrometallurgy operations in Europe leads to surplus black mass being exported to Asia, raising concerns about material security.
THE CHALLENGES TO URBAN MINING
To gain deeper insight into economic perspectives on current and future battery recycling, ADL conducted a research project with RWTH Aachen University in Germany. The project involved interviewing industry experts about the challenges and opportunities for urban battery mining. The results identified six key challenges and cost drivers that need to be overcome.
1. THE HYDROMETALLURGICAL PROCESS
The biggest obstacle to recycling in Europe is the cost of establishing and running hydrometallurgy facilities, as highlighted by two-thirds (66%) of experts. This covers the CAPEX investment required for building complex, specialized facilities capable of handling aggressive chemicals at scale and operating costs. Extracting valuable metals such as lithium, nickel, cobalt, and manganese in battery-grade quality requires precise controls and sophisticated procedures to ensure high-purity recovery. Residues and byproducts include toxic substances and heavy metals, requiring substantial (and expensive) treatment processes to ensure compliance with environmental regulations.
2. BATTERY TRANSPORTATION
There are stringent safety regulations around the transport and storage of EOL or waste Li-ion batteries, some of which are country-specific. Ninety-two percent of experts identified these requirements as challenging because of the high costs they add to battery transportation. A lack of transparency around the condition of batteries (i.e., whether they are simply EOL or have defects) further adds to transport expenses, requiring the greater, potentially unnecessary use of heavy and space-consuming metal containers. Long transport distances, especially over national borders, and lack of experience with safely transporting batteries also add to costs.
3. SITE SELECTION AND PERMIT ACQUISITION
Hydrometallurgical facilities require specific conditions, such as access to sufficient bodies of water, which complicates where they can be located, while the chemical intensity of their processes requires companies to obtain detailed permits for their operation. Securing the right permissions can take substantial amounts of time and requires complex negotiations with regulatory bodies and engagement with local communities and businesses. Permitting and regulations also vary between countries, adding further complexity and potentially leading recycling companies to set up operations in less regulated geographies.
4. SECURING A CONSISTENT SUPPLY OF BATTERIES AND MANAGING UPSTREAM/DOWNSTREAM PARTNERSHIPS
Industry experts see demand increasing for EOL batteries as companies position themselves for the future. Just under half (43%) of respondents perceive securing future return volumes as a significant to enormous challenge because of growing competition. Two factors exacerbate this:
- EV OEMs significantly influence the market, for example, by specifying quantities available for recycling and inviting bids for battery processing. This requires recyclers to navigate complex tender processes — often for short (one-year) contracts — limiting the ability to plan effectively.
- New players, often from Asia or North America, are entering the market. Many have substantial financial resources or experience, meaning they will disrupt market dynamics, potentially through aggressive pricing strategies designed to gain market share.
5. REGULATORY COMPLIANCE AND OPERATIONAL EFFICIENCY
Within the EU, the Battery Regulation mandates minimum recycling rates for specific battery materials, which will progressively increase. Experts believe achieving these targets is technically feasible but will pose a significant operational challenge to recyclers, requiring substantial effort and process optimization to comply. Conversely, increasing recycled content requirements in European batteries will drive the need for recycling.
6. CHANGING BATTERY CHEMISTRIES
Given the significant cost of rare metals, battery manufacturers are looking to alternative battery chemistries that require cheaper inputs. For example, expensive nickel, manganese, and cobalt (NMC) batteries are increasingly being replaced by cheaper new technologies such as lithium iron phosphate (LFP), which contain neither nickel nor cobalt (see Figure 2). LFP is expected to make up 50% of recycling feedstock by 2030. However, recycling profitability is much lower since lithium is the most valuable material that can be extracted from LFP batteries besides the lower-value iron and phosphate components. This is a particular challenge in Europe and North America; in Asia, there is an established, profitable market for LFP recycling. New, lower-cost batteries such as sodium-ion may further lower recycling profitability.
RECOMMENDATIONS FOR BATTERY RECYCLING PROFITABILITY
The creation of large-scale circular economies around battery recycling is vital to the green transition, particularly in Europe. While significant challenges exist, focusing on four recommendations helps overcome obstacles around profitability and provides lessons for businesses creating circular economies in other areas.
1. ADOPT A HUB-AND-SPOKE MODEL FOR LOGISTICS
Transporting EOL batteries over long distances is costly and raises safety concerns. By contrast, moving processed black mass is simpler and much less expensive. Consequently, recyclers should adopt hub-and-spoke models for their operations, with multiple local collection points for EOL batteries feeding spokes where initial mechanical processing is carried out (see Figure 3). The resulting black mass can then be transported to accessible central hydrometallurgy hubs for extraction. This model mitigates environmental impacts and bolsters economic efficiencies, streamlining collection, reducing transportation costs (and emissions), and improving safety. Required capital is reduced as the number of hydrometallurgy hubs is minimized.
The two main challenges to this approach are:
- The significant costs of transporting EOL batteries across borders if spokes are located in different countries.
- The reliance on a small number of large processing hubs. Hub failure or overload could paralyze operations, and securing suitable sites of sufficient size is vital to achieving economies of scale.
2. INNOVATE IN TECHNOLOGY AND PROCESSING
Improving current processing techniques and technologies can reduce costs, increase profitability, and optimize operations.
Two-thirds of experts see presorting batteries as an area that needs to be significantly improved. Currently, many recyclers don’t presort before starting to process, creating greater effort later. Presorting enables recyclers to:
- Distinguish between batteries with the same chemistry but different material percentages (e.g., NMC 111 batteries are significantly more valuable because of their higher cobalt content than NMC 811)
- Understand the battery’s condition so it can be processed differently, such as being repaired rather than recycled
Additionally, current recycling processes are not optimized for efficiency or material separation, adding to costs and meaning valuable metals are lost, such as lithium. Innovative technologies offer the possibility of:
- Improving yields
- Reducing energy consumption (and, consequently, costs)
- Substituting biological solvents for more aggressive/higher-emitting chemicals in the hydrometallurgy process, reducing environmental hazards and regulatory requirements
3. USE MACHINE LEARNING AND AI TO OPTIMIZE RECYCLING
Rightsizing operations and managing capacity and utilization are crucial for recycling profitability. AI supports planning optimization through more accurate short-/medium-term raw material price forecasting based on a much wider range of data inputs and advanced simulations. This enables recyclers to flexibly adapt their capacity planning, operations management, and procurement functions. AI also optimizes location planning for hubs and spokes and related transport and logistics.
In operations, better AI-powered analytics can help predict and diagnose battery health, value, and handling risks more accurately in conjunction with tools such as the EU’s proposed battery passport. AI agents trained with large amounts of battery data can enable new recycling methods such as direct recycling of cells or cell components through better diagnostics on a more granular level. Machine learning also supports greater automation to reduce and remove recycling bottlenecks. Cameras for computer vision and robotics to identify packs, their designs, and conditions enable more automated disassembly processes. This will be critical when volumes of EOL batteries grow and recycling facilities are scaled for efficiency.
4. LEVERAGE ECONOMIES OF SCALE
Asian recyclers show the benefits of economies of scale regarding efficiency, yields, and higher profitability. For example, break-even in hydrometallurgy is achievable only with a capacity of at least 20,000 tons of black mass per year, as scaling up quantities doesn’t proportionately increase plant and material costs. Six in 10 experts say European recyclers need to make large-scale adjustments to achieve similar economies of scale. Adopting hub-and-spoke models helps with scale, securing sufficient supplies of black mass to drive profitability.
INSIGHTS FOR THE EXECUTIVE
Embracing the circular economy for profitability, such as around battery recycling, requires businesses to focus on four key areas:
- Build partnerships across ecosystems, often with non-traditional partners: This includes long-term relationships with all types of players along the battery lifecycle to stabilize supply and demand. It is vital not to limit partnerships to pure battery players but to look more widely; for example, to second-life users in the electricity infrastructure industry, providers of advanced battery analytics, suppliers of machinery, and experts in waste collection and logistics.
- Monitor and understand changing regulatory plans and potential subsidies that can help underpin investment: One key driver of recycling businesses is regulatory requirements regarding batteries, such as the new European Battery Regulation. Beyond that, supply chain transparency rules or carbon footprint regulations indirectly impact the choice of processes and materials and can push demand for recycling output.
- Use AI to predict better demand and material prices, enabling more informed and accurate decision-making: Operating and developing in a highly complex and competitive environment, profitable battery recycling operations rely on well-founded decisions. These require the best available data and capable tools to make better predictions and draw smarter conclusions. AI may boost the analytical capabilities of recycling businesses and deliver a decisive competitive advantage in the years to come.
- Plan and invest now when volumes may be low to gain a leadership position for when volumes increase: The Chinese recycling ecosystem shows that starting early and establishing a footprint and credibility is a key requirement for success and profitability. Outside China, the first major materials and chemical incumbents and some large-scale entrants have started to stake claims. New, innovative businesses can still disrupt by finding better ways to deliver profitable and sustainable recycling in this dynamically evolving industry.
Notes
[1] “Lithium-Based Batteries Supply Chain Challenges.” European Commission, accessed September 2024.
[2] Maisel, Franziska, et al. “A Forecast on Future Raw Material Demand and Recycling Potential of Lithium-ion Batteries in Electric Vehicles.” Resources, Conservation & Recycling, No. 192, 2023.
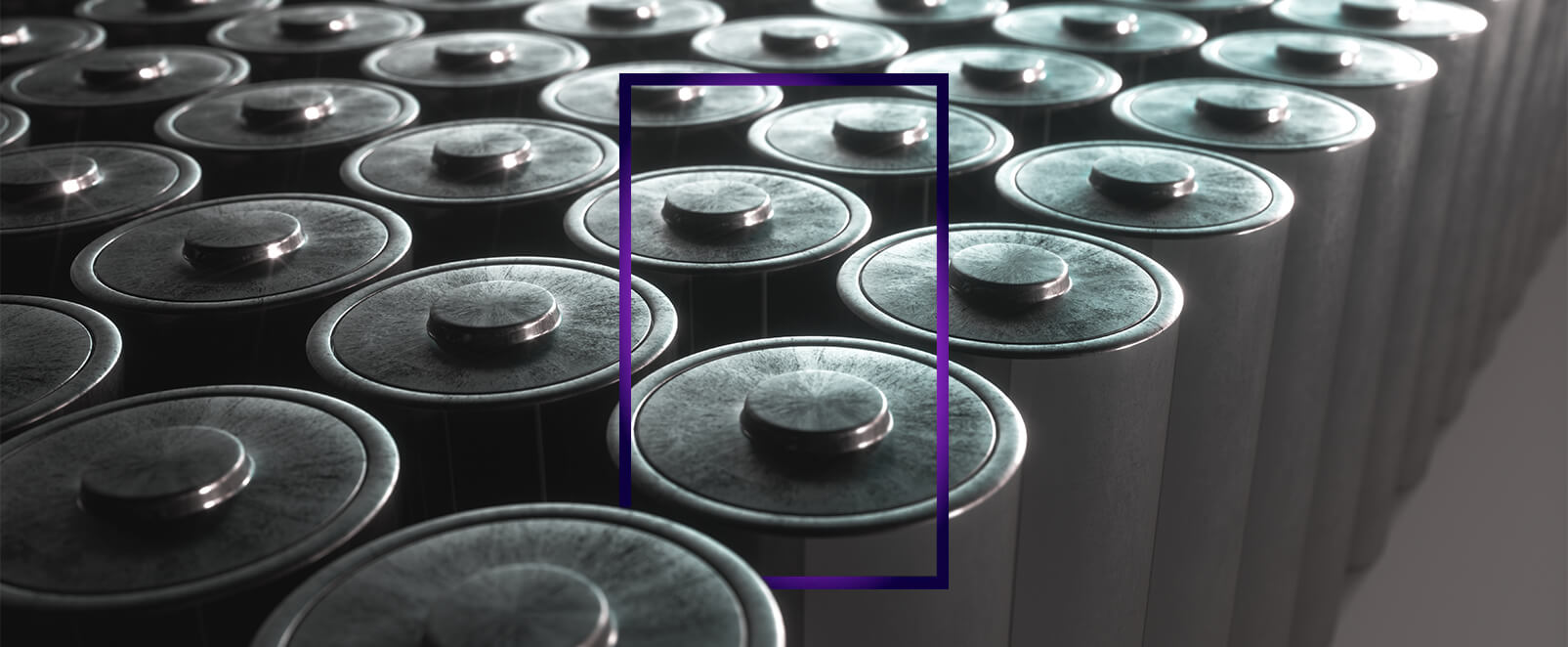
12 min read • Automotive, Sustainability, Technology & innovation management
Opening the urban mine
Building a profitable circular economy based on a lithium battery recycling example

DATE

Creating circular supply chains is essential to the green transition, particularly when it comes to recycling and reusing rare materials. Yet, while many circular economy initiatives may be sustainable, they are not profitable, which hampers their wider development and holds back the achievement of sustainability goals.
Lithium-ion (Li-ion) batteries are a key case in point. Powering electric vehicles (EVs) and renewable energy storage are central to decarbonization and the green transition. According to Arthur D. Little (ADL) forecasts, after surpassing the 1 terawatt hour (TWh) threshold in 2023, global annual Li-ion battery demand will increase to roughly 5 TWh by 2030 and 7 TWh by 2035. However, battery production relies on large amounts of metals (e.g., lithium, manganese, cobalt, and nickel) that generate significant ESG (environmental, social, and governance) risks and carbon footprints when mined, processed, and manufactured. The EU Commission estimates that the global demand for active battery materials such as lithium, graphite, and nickel will double between 2025 and 2030 (see Figure 1). The decade after 2030 will see a further dramatic increase in material demand. However, since the lifetime of batteries in EVs and stationary storage can exceed 10 years easily, the availability of spent batteries for recycling will remain limited during the next decade. For example, in Europe, the material will hardly surpass 1 million metric tons before 2035.[1]
Recycling end-of-life (EOL) Li-ion batteries (from laptops, consumer electronics, and, mainly, an increasing number of EVs) and reusing their components in new batteries should present a clear opportunity to marry sustainability and profitability. The EU Commission expects about half of the demand for nickel and cobalt for batteries in 2040 to be covered by output from recycling facilities.[2] However, in many regions, battery recycling business models are not profitable because of the need for high-CAPEX investments, low current volumes, immature technology, volatile raw material prices, and difficulties in scaling. Over three-quarters (77%) of experts in our analysis agree that recycling EOL Li-ion batteries in Europe is currently not economically viable.
This leads to the unsustainable practice of exporting black mass (partly processed EOL battery materials) to Asia, adding to transport emissions and impacting access to rare minerals required by the growing European battery industry. Global markets reflect this with lower prices for black mass in Europe due to lower local processing capacity, and thus demand, as well as the costs of shipping to Asia.
How can an economically viable circular model be put in place? Based on ADL research of industry players and our experience within client projects, this article sets out a blueprint for urban mining to successfully and profitably recycle Li-ion batteries locally. This template not only helps create a circular economy around batteries but provides best practices that can be applied to other recycling initiatives, such as electronics, plastics, and metals.
BUILDING A CIRCULAR ECONOMY AROUND BATTERIES
The growth of EVs focuses attention on the importance of Li-ion battery production to national and regional economic competitiveness. This leads to an increase in regulations designed to secure supplies of specific materials while governments encourage the creation of battery gigafactories through subsidies and incentives.
THE GLOBAL REGULATORY PICTURE
Regulations around battery recycling and sourcing rare materials vary worldwide but show an overall trend toward stricter standards. Asia, especially South Korea and China, was a notable first mover, with battery recycling regulations in place since 2013. This led to a current recycling rate of approximately 90% and a well-developed, profitable circular economy around batteries.
The EU’s 2006 Battery Directive set a 55% recycling rate target. Realizing this was insufficient, its 2023 Battery Regulation marks a shift toward establishing a closed-loop battery value chain. This includes targets for both recycling particular materials and their reuse in the production of new batteries, including:
- Increasing lithium recycling rates from 50% to 80% between 2028 and 2032
- Increasing cobalt, copper, nickel, and lead recycling rates to 90% from 2028, rising to 95% by 2032
In the US, there is no overarching requirement for battery recycling. However, initiatives such as the Department of Energy’s Lithium-Ion Recycling Prize and programs such as Call2Recycle actively promote and improve battery recycling practices. Furthermore, the Critical Minerals and Materials (CMM) Program indirectly encourages battery recycling by listing certain materials, including cobalt and nickel, as essential for clean technology.
CURRENT CIRCULAR ECONOMY BUSINESS MODELS
Batteries for recycling come from two sources: production scrap from battery gigafactories and EOL batteries from EVs, energy storage, cellphones, and laptops. The average life of EV batteries in first and (less demanding) stationary second-life applications is estimated to reach 10-15 years easily. That means most recyclers focus on batteries from production scrap, especially through closed partnerships between battery manufacturers and recyclers.
This will change in the medium term as EV numbers increase. In Europe, 2030–2035 is forecast to be the cross-over point when EOL volumes from EVs overtake production scrap to form the majority of recycling stock. This will enable new business models, such as vehicle OEMs or battery manufacturers, to retain ownership of the battery materials and use recycling companies as service providers to carry out the extraction process.
In Asia, where battery and EV production picked up earlier, recyclers have already built and begun operating large-scale hydrometallurgy facilities, processing black mass, including from Europe, at scale. This enables more economical operations and has stimulated a strong local market for black mass, resulting in prices around 20% higher than in Europe. The combination of these higher prices and a dearth of current hydrometallurgy operations in Europe leads to surplus black mass being exported to Asia, raising concerns about material security.
THE CHALLENGES TO URBAN MINING
To gain deeper insight into economic perspectives on current and future battery recycling, ADL conducted a research project with RWTH Aachen University in Germany. The project involved interviewing industry experts about the challenges and opportunities for urban battery mining. The results identified six key challenges and cost drivers that need to be overcome.
1. THE HYDROMETALLURGICAL PROCESS
The biggest obstacle to recycling in Europe is the cost of establishing and running hydrometallurgy facilities, as highlighted by two-thirds (66%) of experts. This covers the CAPEX investment required for building complex, specialized facilities capable of handling aggressive chemicals at scale and operating costs. Extracting valuable metals such as lithium, nickel, cobalt, and manganese in battery-grade quality requires precise controls and sophisticated procedures to ensure high-purity recovery. Residues and byproducts include toxic substances and heavy metals, requiring substantial (and expensive) treatment processes to ensure compliance with environmental regulations.
2. BATTERY TRANSPORTATION
There are stringent safety regulations around the transport and storage of EOL or waste Li-ion batteries, some of which are country-specific. Ninety-two percent of experts identified these requirements as challenging because of the high costs they add to battery transportation. A lack of transparency around the condition of batteries (i.e., whether they are simply EOL or have defects) further adds to transport expenses, requiring the greater, potentially unnecessary use of heavy and space-consuming metal containers. Long transport distances, especially over national borders, and lack of experience with safely transporting batteries also add to costs.
3. SITE SELECTION AND PERMIT ACQUISITION
Hydrometallurgical facilities require specific conditions, such as access to sufficient bodies of water, which complicates where they can be located, while the chemical intensity of their processes requires companies to obtain detailed permits for their operation. Securing the right permissions can take substantial amounts of time and requires complex negotiations with regulatory bodies and engagement with local communities and businesses. Permitting and regulations also vary between countries, adding further complexity and potentially leading recycling companies to set up operations in less regulated geographies.
4. SECURING A CONSISTENT SUPPLY OF BATTERIES AND MANAGING UPSTREAM/DOWNSTREAM PARTNERSHIPS
Industry experts see demand increasing for EOL batteries as companies position themselves for the future. Just under half (43%) of respondents perceive securing future return volumes as a significant to enormous challenge because of growing competition. Two factors exacerbate this:
- EV OEMs significantly influence the market, for example, by specifying quantities available for recycling and inviting bids for battery processing. This requires recyclers to navigate complex tender processes — often for short (one-year) contracts — limiting the ability to plan effectively.
- New players, often from Asia or North America, are entering the market. Many have substantial financial resources or experience, meaning they will disrupt market dynamics, potentially through aggressive pricing strategies designed to gain market share.
5. REGULATORY COMPLIANCE AND OPERATIONAL EFFICIENCY
Within the EU, the Battery Regulation mandates minimum recycling rates for specific battery materials, which will progressively increase. Experts believe achieving these targets is technically feasible but will pose a significant operational challenge to recyclers, requiring substantial effort and process optimization to comply. Conversely, increasing recycled content requirements in European batteries will drive the need for recycling.
6. CHANGING BATTERY CHEMISTRIES
Given the significant cost of rare metals, battery manufacturers are looking to alternative battery chemistries that require cheaper inputs. For example, expensive nickel, manganese, and cobalt (NMC) batteries are increasingly being replaced by cheaper new technologies such as lithium iron phosphate (LFP), which contain neither nickel nor cobalt (see Figure 2). LFP is expected to make up 50% of recycling feedstock by 2030. However, recycling profitability is much lower since lithium is the most valuable material that can be extracted from LFP batteries besides the lower-value iron and phosphate components. This is a particular challenge in Europe and North America; in Asia, there is an established, profitable market for LFP recycling. New, lower-cost batteries such as sodium-ion may further lower recycling profitability.
RECOMMENDATIONS FOR BATTERY RECYCLING PROFITABILITY
The creation of large-scale circular economies around battery recycling is vital to the green transition, particularly in Europe. While significant challenges exist, focusing on four recommendations helps overcome obstacles around profitability and provides lessons for businesses creating circular economies in other areas.
1. ADOPT A HUB-AND-SPOKE MODEL FOR LOGISTICS
Transporting EOL batteries over long distances is costly and raises safety concerns. By contrast, moving processed black mass is simpler and much less expensive. Consequently, recyclers should adopt hub-and-spoke models for their operations, with multiple local collection points for EOL batteries feeding spokes where initial mechanical processing is carried out (see Figure 3). The resulting black mass can then be transported to accessible central hydrometallurgy hubs for extraction. This model mitigates environmental impacts and bolsters economic efficiencies, streamlining collection, reducing transportation costs (and emissions), and improving safety. Required capital is reduced as the number of hydrometallurgy hubs is minimized.
The two main challenges to this approach are:
- The significant costs of transporting EOL batteries across borders if spokes are located in different countries.
- The reliance on a small number of large processing hubs. Hub failure or overload could paralyze operations, and securing suitable sites of sufficient size is vital to achieving economies of scale.
2. INNOVATE IN TECHNOLOGY AND PROCESSING
Improving current processing techniques and technologies can reduce costs, increase profitability, and optimize operations.
Two-thirds of experts see presorting batteries as an area that needs to be significantly improved. Currently, many recyclers don’t presort before starting to process, creating greater effort later. Presorting enables recyclers to:
- Distinguish between batteries with the same chemistry but different material percentages (e.g., NMC 111 batteries are significantly more valuable because of their higher cobalt content than NMC 811)
- Understand the battery’s condition so it can be processed differently, such as being repaired rather than recycled
Additionally, current recycling processes are not optimized for efficiency or material separation, adding to costs and meaning valuable metals are lost, such as lithium. Innovative technologies offer the possibility of:
- Improving yields
- Reducing energy consumption (and, consequently, costs)
- Substituting biological solvents for more aggressive/higher-emitting chemicals in the hydrometallurgy process, reducing environmental hazards and regulatory requirements
3. USE MACHINE LEARNING AND AI TO OPTIMIZE RECYCLING
Rightsizing operations and managing capacity and utilization are crucial for recycling profitability. AI supports planning optimization through more accurate short-/medium-term raw material price forecasting based on a much wider range of data inputs and advanced simulations. This enables recyclers to flexibly adapt their capacity planning, operations management, and procurement functions. AI also optimizes location planning for hubs and spokes and related transport and logistics.
In operations, better AI-powered analytics can help predict and diagnose battery health, value, and handling risks more accurately in conjunction with tools such as the EU’s proposed battery passport. AI agents trained with large amounts of battery data can enable new recycling methods such as direct recycling of cells or cell components through better diagnostics on a more granular level. Machine learning also supports greater automation to reduce and remove recycling bottlenecks. Cameras for computer vision and robotics to identify packs, their designs, and conditions enable more automated disassembly processes. This will be critical when volumes of EOL batteries grow and recycling facilities are scaled for efficiency.
4. LEVERAGE ECONOMIES OF SCALE
Asian recyclers show the benefits of economies of scale regarding efficiency, yields, and higher profitability. For example, break-even in hydrometallurgy is achievable only with a capacity of at least 20,000 tons of black mass per year, as scaling up quantities doesn’t proportionately increase plant and material costs. Six in 10 experts say European recyclers need to make large-scale adjustments to achieve similar economies of scale. Adopting hub-and-spoke models helps with scale, securing sufficient supplies of black mass to drive profitability.
INSIGHTS FOR THE EXECUTIVE
Embracing the circular economy for profitability, such as around battery recycling, requires businesses to focus on four key areas:
- Build partnerships across ecosystems, often with non-traditional partners: This includes long-term relationships with all types of players along the battery lifecycle to stabilize supply and demand. It is vital not to limit partnerships to pure battery players but to look more widely; for example, to second-life users in the electricity infrastructure industry, providers of advanced battery analytics, suppliers of machinery, and experts in waste collection and logistics.
- Monitor and understand changing regulatory plans and potential subsidies that can help underpin investment: One key driver of recycling businesses is regulatory requirements regarding batteries, such as the new European Battery Regulation. Beyond that, supply chain transparency rules or carbon footprint regulations indirectly impact the choice of processes and materials and can push demand for recycling output.
- Use AI to predict better demand and material prices, enabling more informed and accurate decision-making: Operating and developing in a highly complex and competitive environment, profitable battery recycling operations rely on well-founded decisions. These require the best available data and capable tools to make better predictions and draw smarter conclusions. AI may boost the analytical capabilities of recycling businesses and deliver a decisive competitive advantage in the years to come.
- Plan and invest now when volumes may be low to gain a leadership position for when volumes increase: The Chinese recycling ecosystem shows that starting early and establishing a footprint and credibility is a key requirement for success and profitability. Outside China, the first major materials and chemical incumbents and some large-scale entrants have started to stake claims. New, innovative businesses can still disrupt by finding better ways to deliver profitable and sustainable recycling in this dynamically evolving industry.
Notes
[1] “Lithium-Based Batteries Supply Chain Challenges.” European Commission, accessed September 2024.
[2] Maisel, Franziska, et al. “A Forecast on Future Raw Material Demand and Recycling Potential of Lithium-ion Batteries in Electric Vehicles.” Resources, Conservation & Recycling, No. 192, 2023.