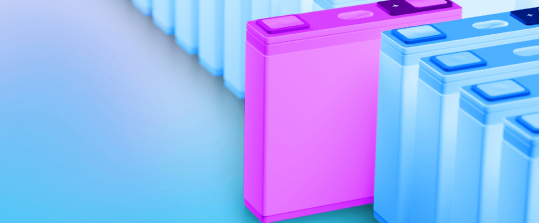
India is one of the largest automotive markets in the world, with demand only expected to rise in the coming years. With government’s push and increasing customer acceptance, electric vehicles (EVs) are gaining significant traction. However, for EV batteries, India remains largely dependent on imported lithium-ion (Li-ion) cells owing to limited local manufacturing capacity and a scarcity of raw materials. Only a collaborative approach from government and industry will allow India to conquer these challenges, become a leader in the e-mobility value chain, and realize its larger dream of rapid and wide-scale electrification of mobility.
INDIAN EV LANDSCAPE: AMBITION & REALITY
Since the launch of the Reva electric car in 2001, India has come a long way in its e-mobility journey. EV demand picked up pace in 2017 with several new electric two-wheeler (2W) OEMs appearing on the market landscape and some of the established passenger car OEMs like Tata Motors and Mahindra foraying into electric cars. FY2022 saw over 420,000 EVs sold in India, a significant jump from 130,000 in FY2021 and 160,000 in FY2020. Quite notably, India clocked monthly EV sales of 50,000 units across all vehicle segments for the first time in December 2021, as per the VAHAN dashboard.
Lower total cost of ownership (TCO) compared to internal combustion engines (ICEs), rising fuel prices for ICE vehicles, reductions in battery prices, and development of charging infrastructure are some of the key factors contributing to this growth. With greenhouse gas (GHG) emission targets in mind, the government has set steep targets for EV adoption across vehicle segments and is also pushing for EVs through favorable policies like Faster Adoption and Manufacturing of Hybrid & Electric Vehicles (FAME II) and production-linked incentive (PLI) schemes. Subsidies and incentives by several state governments are providing further impetus for EV adoption.
However, in the global context, the current e-mobility picture in India does not look very promising. The country is far behind in EV adoption compared to some of the western markets. India’s EV dream faces a multitude of challenges, and high import dependence for Li-ion cells is the most significant one. With very limited domestic production of Li-ion cells, Indian OEMs and ultimately customers must pay higher prices, as battery constitutes ~40% of the total EV cost (see Figure 1). This makes the entire EV industry highly vulnerable to global supply chain disruptions.
DOMESTIC CELL MANUFACTURING —WHERE DOES INDIA STAND?
India’s Li-ion battery demand is currently 3 GWh and is set to grow to 20 GWh by 2026 and 70 GWh by 2030, according to Arthur D. Little (ADL) estimates. Currently, the Ministry of Mines reports that India imports almost 70% of its Li-ion cell requirement from China and Hong Kong. Because cells are the most critical part the of e-mobility value chain (see Figure 2), overdependence on imports is a barrier for the growth of India’s EV industry. Multiple factors, such as limited local manufacturing capacity and finite access to raw materials, refining capacities, and so on, are responsible for this import dependence. However, there have been recent developments in local industry with some of the OEMs, traditional battery players, and new age technology-led start-ups venturing into cell and battery manufacturing.
TDS Li-ion Battery Gujarat is India’s first large-scale Li-ion battery manufacturing plant. Exide Industries has recently partnered with China’s SVOLT Energy Technology for Li-ion cell manufacturing, with plans to invest US $770 million for a greenfield cell manufacturing facility with a 12 GWh capacity. Additionally, Amara Raja has opened the country’s maiden technology hub to develop Li-ion cells at its Tirupati facility in Andhra Pradesh.
OEMs are also gearing up their in-house battery capabilities. For example, Lucas TVS signed an agreement with US-based Li-ion battery technology company 24M Technologies to set up a gigafactory in Chennai to produce cells with 24M’s patented design. Ola Electric invested in a 50 GWh battery manufacturing plant and made a strategic investment in StoreDot, an Israeli battery technology company that is pioneering extreme fast-charging chemistries.
Technology-led start-ups are also gearing up in the Li-ion space. For example, Log9 Materials, a Graphene nanotechnology player, has developed advanced energy storage technologies, claiming 15 minutes for full charging of an electric 2W as well as 15-year-long battery life. In addition, Cell Propulsion, an electric mobility start-up, is developing vertically integrated indigenous e-powertrains (e.g., proprietary components such as battery packs, motor drives) for e-commercial vehicles.
Government is also playing its part by providing a necessary push for localization of cell manufacturing. Beyond the FAME I and FAME II policies for comprehensive growth of EV demand and development of the ecosystem, the government has launched focused schemes to increase domestic availability of batteries, drive down the cost of energy storage, and substitute imports worth $3 billion every year. Through the PLI scheme for Advanced Chemistry Cell (ACC), subsidies of INR 18,000 crore are being offered for greenfield battery manufacturing facilities. In the recently conducted bid process for PLI ACC, Ola Electric (20 GWh), Hyundai Global Motors (20 GWh), Reliance New Energy Solar (20 GWh), and Rajesh Exports (5 GWh) have won subsidies.
However, efforts by both the government and industry may not be enough to cater to the exponentially growing demand as the industry faces some critical challenges in localizing the supply chain for EV batteries. India so far has not developed indigenous EV cell technologies at scale. Globally, players like Panasonic, LG Chem, or Tesla have spent billions of dollars on continuous innovation and R&D for cells and EV batteries, while established Indian battery players have been laggards in this area. Developing indigenous cell technology and batteries suitable for Indian climatic conditions is critical for both increasing affordability and safety.
Another key challenge is India’s poor access to the key raw materials lithium, nickel, cobalt, and manganese, which account for over 80% of the cell cost (see Figure 3). The natural reserves for these materials are concentrated in just a few countries across the world, with poor access for Indian players (see Figure 4). Additionally, India lacks adequate refining capabilities for these materials.
Localizing the Li-ion battery supply chain is essential to India’s ambition of becoming self-sufficient in cell manufacturing and putting it on the world map as a significant global Li-ion battery manufacturer and exporter.
HOW CHINA ACED ITS WAY TO LI-ION BATTERY LEADERSHIP
China has aggressively expanded in the EV battery space over the last 10 years, conquering each part of the supply chain to emerge as the dominant player in e-mobility (see Figure 5). Once a laggard in traditional ICE vehicles, China now leads in next-generation EVs (see Figure 6). Large investments in R&D, favorable government policies, foreign direct investment inflows, and aggressive acquisition of raw material resources across geographies were key enablers for China’s spectacular growth in Li-ion batteries (see Figure 7).
Although China has limited natural reserves of these crucial elements, Chinese companies have bought mines in countries with these resources, directly exporting them back to China. For example, China’s Contemporary Amperex Technology Co. (CATL) and Tianqi Lithium are among the biggest buyers of lithium mines and refine two-thirds of the world’s supply of lithium. In Indonesia, China’s Tsingshan Holding Group operates the world’s largest nickel syndicate. Further, Bloomberg reports that in 2017, Chinese firms owned eight out of the 14 largest cobalt mines in the Democratic Republic of the Congo. Such resource acquisition has made Chinese firms independent, giving them complete control of the supply chain. Moreover, leading Chinese player CATL has invested heavily in R&D and, according to CnEVPost, plans to invest an additional $440 million to build smart factories and R&D facilities dedicated to battery and smart technology development.
Government policies have played a crucial role in furthering battery technology innovations and manufacturing in China. In October 2021, when the price of cobalt shot up by over 30% in global markets and the price of lithium carbonate almost doubled, the Chinese government increased the tax rebates for cathode battery scrap from 30% to 50%, making recycling of batteries more attractive. China has also seen large investments in battery manufacturing from Western companies, whether it’s the Tesla Gigafactory in Shanghai or Volkswagen’s investments in battery makers Guoxuan High-Tech Co. and JAC Motors. The Chinese government has ensured the right attention and interest from foreign players through appealing policies and incentives.
EUROPE’S PUSH FOR BATTERY SUPPLY CHAIN LOCALIZATION
Despite lagging behind China in terms of regional lithium supply chain growth, Europe has been drawing more investments than China since 2019. The European Battery Alliance was founded in 2017 to assist Europe in developing a competitive supply chain, and Europe is now targeting to become self-sufficient in providing lithium for EVs. In addition to economic and political drivers for Europe’s efforts, there is also a technical rationale. As cathodes are susceptible to weather conditions and moisture, long transit durations in hot climatic conditions are best avoided, making local regional supply chains more important. Global supply chain disruption during the pandemic has further accelerated the shift toward localization.
Nordic countries are playing a vital role in Europe’s efforts to localize battery supply chain, with Finland soon becoming home to one of the world’s largest nickel and cobalt sulphate refineries. Umicore and BASF, manufacturers of battery materials, have both made investments in Finland. For its part, Northvolt commissioned its Swedish facility in 2021 and batteries from this first European-owned GWh-scale cell factory have been rolling off the production line ever since. Beyond the Nordics, Britishvolt is also constructing the UK’s first gigafactory for EV batteries.
HOW CAN INDIA EMERGE AS LEADER IN EV BATTERY PLAY?
To realize the vision of becoming self-sufficient as well as a leading exporter of Li-ion batteries, India must overcome several barriers that would require a concerted effort from government and industry, and, as the most critical part of the value chain, cell manufacturing needs to be the primary focus.
Government’s role cannot be stressed upon enough if India wants a place on the world map of EV industry. The Indian government will have to work on multiple fronts to localize the supply chain for batteries, including enabling better access to raw materials like lithium, cobalt, manganese, and nickel for domestic manufacturers.
Taking lessons from India’s neighbor in the north, improved access to raw materials can be provided in multiple ways, including reduction of import duties on raw materials, improving bilateral ties with countries rich in natural resources of the raw materials, and encouraging Indian companies to acquire those resources. Providing incentives to local players to build refining capabilities, promoting sustainable domestic graphite mining with relaxation of stringent regulatory restrictions, increasing import duties on cells and batteries, and incentivizing recycling of batteries can provide further impetus to localize cell manufacturing.
To promote large-scale battery manufacturing, the government can also set up special economic zones focused on large-scale gigafactories, with a range of manufacturing-related subsidies, continuing with PLI schemes for battery players, inviting and incentivizing foreign players to invest and build capacities in India, and providing export incentives for cell and battery producers. As many players around the globe look to a China Plus One strategy to reduce their dependence on China due to geopolitical and supply chain reasons, the Indian government must put a strong foot forward and provide those companies with compelling reasons to consider India as a manufacturing and sourcing base.
The government of India has already started taking steps in the right direction, including committing to invest $6 million jointly with the Australian government to explore lithium and cobalt mines in Australia, increasing custom duties on the import of Li-ion cells from 5% to 10%, the aforementioned incentives under the PLI scheme for gigafactories, and so on. These efforts will surely go a long way in localizing the battery supply chain.
At the same time, industry players must gear up to make their mark on the EV landscape. While battery players are forming alliances and partnerships with global technology players, they should also invest in continuous R&D to improve cell chemistries and battery design that is more suitable, safer, and more economical in the Indian context. Advanced cell chemistries like sodium-ion, metal-air, and the like, where raw material availability is better in India, potentially can be further developed and commercialized at large scale. Joint ventures and acquisitions can also be explored to acquire the capabilities as well as the robust talent needed in the battery space.
Apart from battery players and OEMs, metal and mining companies must also play their part in facilitating access to raw materials. They will need to invest in refining capabilities and acquire resources across the globe if they want to ride the EV wave.
Additionally, Indian players need to benchmark themselves to superior quality and environmental standards to gain brand reputation in the global market. This will help the country become self-sufficient in batteries but also develop India as a global export hub. As both global and Indian OEMs look for green supply chains and pay increasing heed to environmental standards, any player aspiring to build a presence in the battery supply chain must have sustainable operations. This will be particularly difficult because battery production itself consumes a lot of electricity, for which coal is currently the primary source in India.
By 2030, just to serve the local demand of Li-ion batteries, India would need upwards of an estimated $10 billion in investments in cell manufacturing capacity, with additional investments in raw material refining capacities. As a consequence, however, this would create one million or more new jobs in the battery manufacturing and related ancillary businesses and services.
Conclusion
INDIA’S WAY FORWARD
A collaborative approach between the government and industry is the way forward for building a local supply chain for batteries and making India an export hub. Comprehensive policies from the government that encompass the complete battery value chain — from acquisition of natural resources to recycling of batteries — will go a long way in providing a necessary push to the industry. This may include:
- Active efforts with bilateral relationships and investments in countries rich in natural resources.
- Tax subsidies and development of special economic zones/lithium parks across countries to promote investments in raw material refining and cell manufacturing capacities.
- Continued PLI schemes and subsidies for cell manufacturing.
- Regulations for battery usage, secondary applications, and recycling with strong incentives for compliance.
Private players, including established battery manufacturers and automotive OEMs, as well as e-mobility start-ups, need to play their role with investments in R&D, global partnerships, and alliances across the value chain to create a strong supply chain. These efforts, as well as increased demand from end customers, will go a long way in turning India’s EV dream into reality.