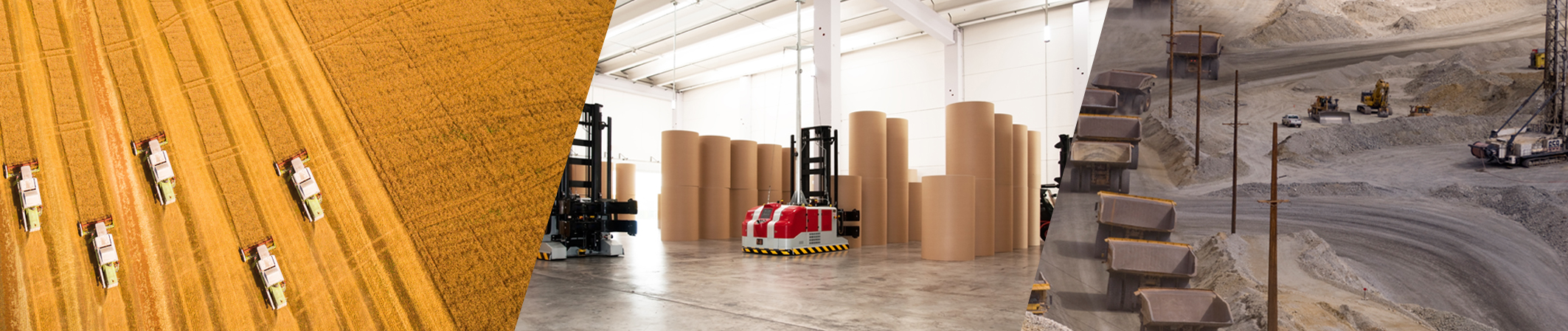
Imagine a field with a fleet of unmanned harvesters or a quarry in which driverless trucks transport rocks. Is this a sciencefiction scene? It actually is not: off-highway (OH) vehicles, primarily or exclusively used on private property, are autonomous pioneers in many ways. All major OEMs develop autonomous machines, and globally, hundreds of vehicles already run driverless in mines, warehouses and, surprisingly, golf courses. A broad ADL study, in which we interviewed 30+ industry and technology experts along the value chain (OEMs, suppliers, distributors and end customers) in Europe, North America and Asia, highlights the biggest challenges, barriers and implications for vehicle design and the industry’s business models.
Machine automation versus autonomy
Vehicle autonomy has become a rather diffused and expansive term, not only for passenger vehicles. In our context, it relates to driverless operation of mobile machinery in the off-highway industry. For analysis, we chose the off-highway sectors agriculture (AG), construction (CON, including mining), lawn and turf care (LTC) and material handling (MH) due to their market potential and pioneer characters.
When is a machine “driverless” or “autonomous”? Partial automation of tractors and harvesters (e.g., auto-steering) has been state of the art for years now. But automation and autonomy are not the same thing. The automation of driving and working functions on an off-highway vehicle is just the enabler of real machine autonomy. We differentiate between four levels of automation and autonomy. The term “autonomous machine” only applies to level 3 and level 4 vehicles which don’t require local operators at all, or at least for major parts of their regular work. Both levels require basically the same hardware.
The most important components are 3D-perception sensors (LiDAR, radar, stereo camera), GNSS (global navigation satellite system) and specific sensors to monitor the custom work functions. Sensor integration and software make the difference and drive the complexity for level 4 autonomy.
Machine autonomy is a hot topic in off-highway industries: more than 90 percent of study participants said autonomous technology was highly relevant for them, 50 percent had already invested in R&D, demonstrators or first projects, and 30 percent were already offering (semi-)autonomous products. R&D is driven mainly from two sides: big OEM and small robotics specialists. Small and mid-sized OEMs mainly monitor development of technology and the market today, and prefer selective technology alliances over proprietary R&D. Users of off-highway vehicles face constant pressure to become more efficient.
In the past, bigger and more specialized machines were the main answer to increasing productivity requirements – a trend that has reached its peak, according to many experts. Machines cannot grow further without costly lightweighting and loss of road usability, and higher specialization only leads to marginal effects. To reach the next productivity level, new concepts and technologies are crucial.
Autonomy is one answer: it addresses requirements such as 24/7 operation, higher productivity, reliability and predictability. High-utilization use cases in high-labor-cost countries are the perfect application for autonomous machines (e.g., forklifts in huge warehouses or golf course mowing), as they help to reduce labor costs and the number of accidents.
Operator safety and health are major drivers for autonomous machines in mining and quarries. Operators are kept out of heat, humidity, dust and dangerous environments. Sending fully autonomous machines is the next logical step after remote operation, and also the objective of mining companies today.
Technology is ready, but the high costs still outweigh the benefits at the moment!
– Mining user
In LTC and MH, fully autonomous machines (levels 3 and 4) are available today for special applications, but the majority are scarcely equipped with assistance systems. Agriculture and construction stand out: they apply machines with advanced operator assistance systems (level 2), but a very limited number of vehicles reach level 3 autonomy.
Why don’t we see more autonomous machines at work today? According to industry experts, the business case has to turn positive. Autonomous machines are still too expensive in TCO for the majority of use cases. Luckily, the off-highway sector can benefit from R&D investments and technical progress in the automotive industry. Once costs of high-performance components and systems decrease in a more mature market, other hurdles will be taken more easily. Reliability and productivity potential of autonomous solutions can only be fully exploited with affordable yet capable sensors and, most importantly, software and a high-performance back end. Only reliable and economic solutions will convince users.
The current lack of legal norms and standards for autonomous machines seems to be only a minor concern. The industry takes a pragmatic approach: no legislation or regulation stops the operation of autonomous machines on private and closed areas, and technical standards fill the regulatory void in many cases. Nevertheless, the regulatory void has a negative impact on the market uptake, especially in AG, with many use cases in semiclosed areas (e.g., children playing in cornfields). Special laws and regulations are expected only once we see a significant number of autonomous machines in operation.
The main customer requirement is always reduced costs – safety alone won’t sell these machines
– AG/CON OEM
Autonomous machines are tools to earn money, and users from all industry segments want lower total cost of operation (TCO) and ownership compared to manually operated counterparts. Increasing safety and reliability are particularly relevant in selected industries, to protect both workers (mining) and products and goods (e.g., agriculture, material handling). Some users even need to address severe labor shortages in their industries and try to increase flexibility with autonomous machines.
In many industries using off-highway machines, the expected amortization time is around two years, while the machinery is typically used for three to five years. Autonomous machines fulfill these requirements in only a few applications today.
Autonomous “pioneer” applications of today and the near future have similar characteristics:
- High utilization duty cycle.
- Operation in a closed-off work environment.
- Single and simple work function.
- No on-road use and no road-traffic homologation.
Typical examples of use cases that fulfill these requirements are autonomous mowers at golf courses (e.g., the Turflynx F315), autonomous lift trucks in warehouses (e.g., Linde Matic trucks by Balyo) and autonomous haulage systems in mines and quarries (e.g., solutions from Caterpillar, Komatsu, ASI).
If the warehouse has an intelligent design, break-even is possible in less than one year!
– MH OEM
For an autonomous forklift, for example, a positive ROI can be reached in less than a year due to 24/7 operation, although the additional technology costs for the autonomous system are four times the vehicle base price. But those cases are still hard to find. Most study respondents ask for an additional cost reduction of approximately 50 percent from today’s level. To meet this goal by 2025, an annual cost reduction of approximately 10 percent for the base technology components is required. Price developments in the automotive industry (e.g., for radar, solid-state-flash LiDAR) indicate that an annual improvement by 10 percent or more is very likely, supported by increasing demand and new players entering.
Depending on specific applications and their requirements, the market for autonomous machines will develop quite differently across industry segments. The broad market uptake of autonomous machines is expected around 2025, when technology costs and customer acceptance will reach reasonable levels. Until then, pioneer applications with significant volumes will be found only in material handling and lawn and turf care.
Material handling as a front-runner, with autonomous machines already in operation today
Material handling will be the major application of autonomous machines until 2030. Autonomous lift trucks in warehouses are not only market ready, but already in operation today. These trucks no longer require fixed infrastructure, as older AGVs (automated guided vehicles) have, but instead rely on an environmental recognition system updated in real time. The MH sector is currently the only sector with an existing regulatory framework for autonomous industrial trucks, since 1997. But the high functional safety requirements (Automotive Safety Integrity Level (ASIL) D) are also a barrier to applying the autonomous lift trucks in areas with human traffic or outdoor environments. End users expect “more than 99.9 percent reliability and 0 percent failure”, and currently the technology can’t provide this.
Little relevance for operator assistance in lawn and turf, end users demand level 4 autonomy
Lawn and turf care (LTC) is a very specific segment of the off-highway industry. Due to the relatively low vehicle size and price, the human is by far the biggest share of operating costs (approximately 70 percent), at least in high-labor-cost countries. Operator assistance functions such as lane-keeping assistance do not render enough benefits to justify the additional costs. The solution is to either replace the operator with Level 4 automation or have no automation at all.
Agriculture: High-efficiency farming is targeting level 3 autonomy
Market uptake in agriculture will follow around 2025, with a significant number of applications mainly targeting level 3 autonomy due to special industry requirements and more complex work environments and functions. Due to its significant market size, AG is nevertheless expected to become the biggest segment for autonomous machines after 2030. Increasing productivity per acre remains the major objective. Three trends currently shape the industry:
- Digital farming: Data-driven farm management systems steer operations. Autonomous machines collect the required data and operate on predefined programs.
- Precision farming: Systems minimize the input of seeds, herbicides and fertilizers, and maximize the output by precisely timed crop treatments and harvesting. High levels of machine automation are required, e.g., in seeding, spraying and harvesting.
- Multi-machine operation: An operator may be required for failure handling, but multi-machine operation will be the dominant future approach. Platooning concepts are already available today. Industry experts expect a significant share of level 3 vehicles by 2025.
CON is very challenging for high autonomy; only niche applications are expected
In construction, autonomous machines will play a minor role in the near future. Except for certain niche applications, such as haulage trucks, the vast majority of vehicles will stay at level 2 in the next 10–15 years. CON offers the most difficult environment for autonomous technology: complex and dynamic construction sites and machines that are used for limited amounts of time at changing locations. Many processes on construction sites require exact interplay between several machines, and therefore autonomy would be required for all machines in the network. Additionally, many machines are multi-purpose, and smaller auxiliary machines, in particular, often have very low utilization. Big OEMs will mainly focus on operator assistance. Expected niche applications of level 3+ autonomy are roller compactors for road building, high-power loaders with high utilization, and autonomous haulage systems in mines and quarries.
Our equipment will stay big until 2030 because all of it is optimized for big machines
– AG industry expert
Although the first machines will have autonomy as an additional feature, with autonomy levels 3 and 4, machines will no longer need operator cabins and a completely new vehicle design will become possible: current vehicles are built around the driver’s cabin, including the seat and controls. Additionally, many mechanical components can be replaced by electrical components (e.g., for steering), and sophisticated comfort and safety features (e.g., suspension) will become obsolete. This could decrease the vehicles’ bill of materials significantly and balance the additional items for autonomous technology.
But until 2030, insignificant changes in vehicle design across offhighway industries should be expected. Vehicle size is directly linked to power requirements, especially in CON and MH.
In AG today the value chain is optimized for large machines, and reverse development will take some time. LTC will probably see the biggest change in vehicle design. Robotic household mowers give a good indication on a small scale of how the look of a conventional ride-on mower will change. The most important change in vehicle concepts across all industries will not be the removal of the cabin, but increasing electrification of the machines. Electrification makes automation a lot easier and more cost-efficient, with benefits in precision, steering and simulation. Together with stricter emissions regulations, this leads to an expectation that small machinery will be completely electric by 2030 and bigger machinery will at least become hybrid.
Outlook: Autonomous technology opens the door for new players and business models in the off-highway industry
Small and medium-sized OEMs, in particular, are currently struggling with developing their own autonomous technology due to the enormous resource requirements. Third-party technology providers fill the gap that hesitant OEMs create, and either target the end user directly with retrofit solutions or offer white-label solutions through OEM or distributor partnerships. Their co-development approach is more flexible and often cheaper than a solution delivered end-to-end by a single OEM. Specialized suppliers and technology start-ups are natural M&A targets for OEMs to grow and build up relevant capabilities.
Autonomous machines not only require new technology competencies, but also new sales channels and formats: new business models will arise. The trend toward precision farming is a good example: it is a plausible hypothesis that farm equipment OEMs will extend their businesses, becoming solution providers as autonomous machines combine the previously separate areas of vehicles and operation. This will allow OEMs to shift parts of the value creation from farmers to themselves. In this business model, software and data ownership remains with the OEM. The service is offered as a free platform, but keeps the farmer in the OEM “ecosystem”. John Deere is the clear frontrunner OEM in this development, facing competition from AG-chem giants (Monsanto & Co), which are also expanding their digital farming ecosystems.
Conclusion
Autonomous machines will change to the fast lane, and in 2025 we can expect significant demand from agriculture, material handling, and lawn and turf care for selected applications. Industry players such as vehicle OEMs, suppliers and fleet operators need to act now.
Technologically, electrification, connectivity and digitalization support the development of autonomous machines, and vice versa. These synergies help players that already have developed competencies in robotics, automation and actuation, sensors, high-precision navigation, and the like.
Incumbents and new entrants have to decide today what part of the new ecosystem they want to occupy, and how. Regardless of whether they make, buy or partner, investments and transformation seem inevitable for them to stay in the game and avoid missing a great opportunity to reshape the off-highway vehicle industry.