9 min read • Digital problem solving, Strategy, Technology & innovation management
Simulating strategy
The real potential of the Industrial Metaverse
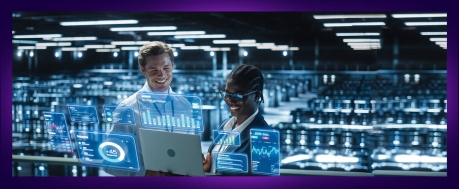
Is the Metaverse dead? With the same rapidity that it was hyped up only a couple of years ago, today it has fallen from grace. So far, most people have failed to get excited about the idea of spending large amounts of time withdrawn from the real world wearing clunky goggles. Now, it’s all about artificial intelligence.
So, should businesses just drop the Metaverse, or at least put it on the back burner, and focus on AI instead? Recent work by ADL’s Blue Shift institute on the Industrial Metaverse – that is, metaverse applications for business, rather than consumers – strongly suggests that businesses would be unwise to do so.
In this article, we explain what the Industrial Metaverse really means, its key building blocks, the business value it can deliver, and what companies should do about it. The summary provided here is based on a comprehensive Blue Shift study conducted in early 2023, comprising in-house research, client experience, and contributions from simulating interviews with experts across industry and academia.[1]
What’s new about the Industrial Metaverse?
Most people understand that the Industrial Metaverse is concerned with the use of virtualization to conduct various industrial tasks better, aimed at delivering benefits such as greater operational efficiency and effectiveness, reduced costs, and better quality.
However, views differ about whether the Industrial Metaverse is a genuinely new concept, or instead just a new label for existing digital technologies under the Industry 4.0 umbrella that have been around for a long time (Figure 1).
Industry 4.0 refers to the “fourth industrial revolution,” and was first coined in 2015 to capture the transformational impact of cyber-physical systems. As shown in Figure 1, some of the technology blocks that are part of Industry 4.0 are also highly relevant for the Industrial Metaverse, including AI, connectivity, cyber/physical systems, blockchain, virtual workplace, and digital twins. In fact, virtual models, simulations, and digital twins of factories and plants have been around for nearly a decade, and digital design tools even longer. Virtual training, such as training for airline employees, is also well established. Significant improvements in productivity and efficiency, up to double-digit percentages, have been demonstrated in existing applications.
That said, implementation of Industry 4.0 is still by no means as widespread as was expected a decade ago. It faces several common barriers, including high upfront investment, difficulties in coordinating the required cross-functional transformation, challenges in data security and management, lack of available skills, and limitations imposed by legacy IT systems.
So, what’s new about the Industrial Metaverse? What’s new is a convergence of key technologies leading to a step-change in simulation capabilities (Figure 2).
Up until now, digital twins have been mainly limited to discrete products, components, plants, or factories. Use cases have been mainly targeted at operational and maintenance performance improvement. Further developments in simulation of complex systems, data visualization, and AI, combined with ongoing improvements in connectivity (IoT) and collaboration technologies, supported by increasing computing power, mean digital twins are now becoming possible for multiple connected facilities and systems.
This extends and elevates digital simulation from the level of operational improvements and design aids, towards becoming a key tool for strategic decision-making across complete systems – and ultimately across an entire global industrial enterprise.
Some early examples have already been shown: BMW’s iFactory program involves simulation of potentially all its production facilities to enable a complete production strategy based around the use of digital twins for all production sites.
Perhaps even more impressively, Michelin has applied digital twinning together with complex system modeling to optimize its global sourcing strategy. (See Box 1.)
How best to conceptualize it
Based on this idea of a step-change in simulation capabilities, we can usefully define the Industrial Metaverse as follows:
“A connected whole-system digital twin with functionalities to interact with the real system in its environment, allowing decision-makers to better understand the past and forecast the future”
Figure 3 shows its primary functional and technology building blocks.
At the core is the “whole-system digital twin,” which ultimately could represent a complete end-to-end industrial system, including not just physical assets, but also processes, functions, resources, and organization. It would extend beyond the company boundaries to include relevant players and interactions across the whole company partner ecosystem, both upstream and downstream. It could also eventually include the broader environment within which the company operates. It needs to be constructed as a complex system to enable realistic and dynamic system behaviors to be modeled. Extensive “what-if” simulation functionality is a key part of the twin. Simulations are based on not just past data, but also present and future data.
Four key functions are necessary for the system to operate:
-
Connect: The digital twin is permanently connected to the real-world system through the IoT (for “hot” current data) and ERP systems (for “cold” stored data). Real-time bidirectional connections enable continuous data collection and actuation back onto the system.
-
Compute: The capability to process very large data volumes from the real system, including analytics, complex system modeling, pattern recognition, and simulation, to enable future scenario formulation.
-
Conceive: Visualizing both physical and non-physical data, which may or may not be fully immersive. These visualizations interpret and present complex data in different ways, not only to simulate reality, but also to facilitate understanding and illustrate “what-if” scenarios.
-
Collaborate: Functionality to enable a range of interactions, between internal staff, ecosystem partners, value chain players, customers, and others. Interactions may include commercial transactions as well as everyday co-working.
Figure 3 shows five key technology building blocks that enable this functionality, supported by a sixth computing capability technology block. These technologies, for the most part, exist already. However, further development is needed in all of them to deal with the increasing scale and complexity of data. Increased computing capability itself is a critical enabler for achieving very large, connected digital twin simulations.
Overall, the picture suggests a timescale of five+ years before true connected whole-system digital twins will be feasible, although in the meantime, intermediate steps involving digital twins of increasingly complex systems (such as the Michelin global sourcing example above) are still possible.
Why should companies pursue the Industrial Metaverse?
1. Conventional strategic decision-making is becoming inadequate to meet the combined challenges of complexity, acceleration, cognition, and sustainability
The last few years have seen a mushrooming of complexity in industrial systems – for example, in the last two years alone, the volume of enterprise data has risen by over 40 percent to more than two petabytes, with vastly increasing partner network complexity. At the same time, the pace and unpredictability of change is accelerating. The limitations of human cognition mean making good decisions within these faster-moving, unpredictable systems is difficult. Even more importantly, sustainability imperatives mean end-to-end complex industrial system control is becoming increasingly important, for example, to manage Scope 3 emissions and develop strategies to achieve net-zero growth.
Conventional strategic decision-making is poor at meeting these challenges because it typically relies on oversimplification of complex systems. This means it often misses unexpected system impacts, and can be lagging rather than leading, failing to anticipate and react fast enough to rapid changes. The Industrial Metaverse offers the possibility of allowing companies to take informed C-level decisions based on a dynamic, forward-looking, whole-system approach. This would identify performance improvements and the impacts of change more rapidly and effectively, as well as help deliver on obligations to manage overall impacts and achieve sustainable growth.
2. The business benefits of the Industrial Metaverse, even in the short-term, are significant
As we have noted, even if fully connected, whole-industrial-system digital twins are some years away, organizations can still reap significant benefits from existing applications, many of which overlap with Industry 4.0.
Today’s use cases can be split into four categories:
-
Optimization: e.g., improvements in operation and maintenance, product quality, supply chain, and customer service
-
Training: e.g., operational staff, safety, remote, and product training
-
Technical tools: e.g., design/construction integration, asset inspection/maintenance, and remote troubleshooting
-
Management tools: e.g., virtual meeting, collaboration, transaction, and interaction tools
As digital twins extend beyond discrete plants towards industrial systems, the benefits will surpass productivity and efficiency to include the potentially much greater impacts of better strategic decision-making on overall growth, margin, and shareholder value.
3. The Industrial Metaverse market could accelerate rapidly in a five+ year timeframe
Predicting when technologies will accelerate is always difficult. The sudden explosion of AI, together with advances in complex systems simulation, data visualization, and connectivity, could act as a catalyst. Importantly, unlike with the consumer Metaverse, adoption does not depend on acceptance of immersive virtual environments. Reflecting this key point, Apple’s CEO, Tim Cook, prefers to use the term “spatial computing” rather than “Metaverse.”
The current Industrial Metaverse market size is in the USD100–150 billion range (depending on how you define the scope). Our conservative forecast is that it will grow to around USD400 billion by 2030, although the upside could be more than USD1 trillion, with a CAGR in the 20–30 percent range.
Insights for the executive – What should companies do now?
Companies need to consider their strategy for the Industrial Metaverse in the context of their broader digital transformation journey. Organizations cannot easily “leapfrog” to full Industrial Metaverse implementation unless digitalization is already fairly mature. We suggest four steps:
1. Review digitalization strategy, journey, and position
As a starting point, companies need to have a clear vision and pathway for their overall digitalization journey. Understanding the current position on the digitalization journey helps to determine:
-
What still needs to be done in terms of digitalization basics before embarking on Industrial Metaverse development (such as data availability and infrastructure)?
-
What is a realistic pace of development going forward?
-
What would be a feasible target destination to align with the rest of the digitalization journey?
2. Identify value-adding opportunities and develop a roadmap
Many applications and use cases already exist. In developing the roadmap, companies should consider:
-
What potential applications and use cases would add the greatest value? The initial applications for the Industrial Metaverse are likely to be operational, with an aim to extend towards more strategic applications over time.
-
What is already technically feasible today, versus potentially feasible in coming years? As we have seen, although many feasible opportunities are currently available, large-scale complex industrial system simulations are still some way off.
-
What is the vision and ambition for Industrial Metaverse applications in a five+-year time frame? The scale of ambition may depend upon the scale of digital transformation that companies are already committed to.
In developing the road map, companies should avoid overambitious detailed modeling at the start, as this could stifle early progress. As well as the use cases themselves, the roadmap should consider what new processes are needed to access, update, analyze, interpret, and act upon the required data.
3. Implement pilots, adopt a test-and-learn approach, and manage change proactively
An agile and responsive test-and-learn approach will work best. This means starting small and selecting initial pilot projects that are readily replicable, with relatively short payback times that do not need extensive involvement from external stakeholders. Managing the people impacts of implementation is key, for example, new roles and skills requiring support over an extensive period.
4. Build and align the partner ecosystem, creating a win-win
The major benefits of the Industrial Metaverse are realized through involving not only internal operations, but also the partner ecosystem. This requires sharing of much more data than is traditionally shared between commercial partners, which demands a new mind-set and culture. Mutual benefits should be clearly demonstrated – such as faster customer response, reduced working capital, smoother customer/supplier interfaces, and better management of sustainability impacts. Data management standards and adequate safety and security are also key.
The Industrial Metaverse has tangible business value beyond the hype. Executives should not write it off just yet.
Note
[1] ADL/Blue Shift report The Industrial Metaverse – Making the invisible visible to drive sustainable growth (2023)
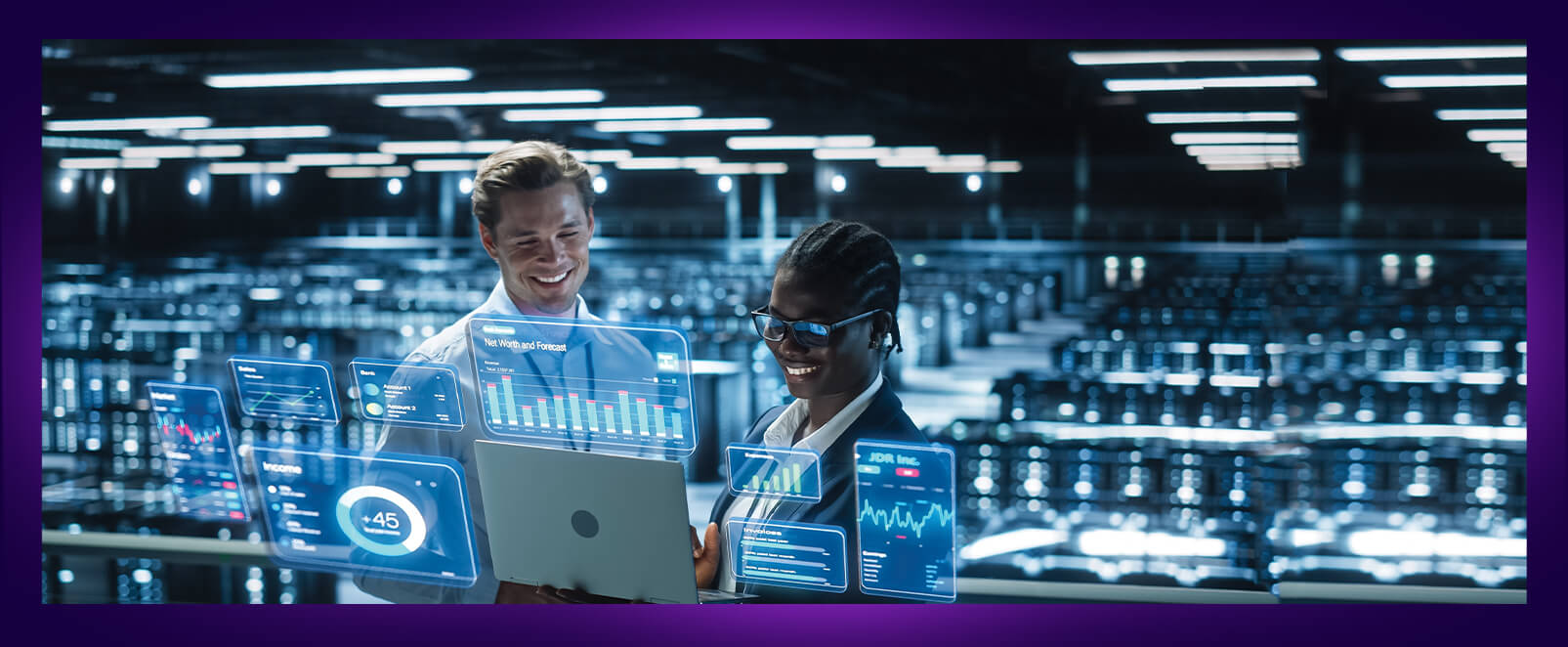
9 min read • Digital problem solving, Strategy, Technology & innovation management
Simulating strategy
The real potential of the Industrial Metaverse
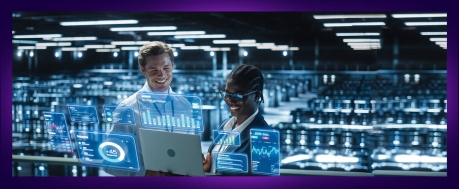
DATE
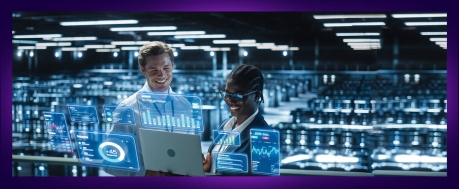
Is the Metaverse dead? With the same rapidity that it was hyped up only a couple of years ago, today it has fallen from grace. So far, most people have failed to get excited about the idea of spending large amounts of time withdrawn from the real world wearing clunky goggles. Now, it’s all about artificial intelligence.
So, should businesses just drop the Metaverse, or at least put it on the back burner, and focus on AI instead? Recent work by ADL’s Blue Shift institute on the Industrial Metaverse – that is, metaverse applications for business, rather than consumers – strongly suggests that businesses would be unwise to do so.
In this article, we explain what the Industrial Metaverse really means, its key building blocks, the business value it can deliver, and what companies should do about it. The summary provided here is based on a comprehensive Blue Shift study conducted in early 2023, comprising in-house research, client experience, and contributions from simulating interviews with experts across industry and academia.[1]
What’s new about the Industrial Metaverse?
Most people understand that the Industrial Metaverse is concerned with the use of virtualization to conduct various industrial tasks better, aimed at delivering benefits such as greater operational efficiency and effectiveness, reduced costs, and better quality.
However, views differ about whether the Industrial Metaverse is a genuinely new concept, or instead just a new label for existing digital technologies under the Industry 4.0 umbrella that have been around for a long time (Figure 1).
Industry 4.0 refers to the “fourth industrial revolution,” and was first coined in 2015 to capture the transformational impact of cyber-physical systems. As shown in Figure 1, some of the technology blocks that are part of Industry 4.0 are also highly relevant for the Industrial Metaverse, including AI, connectivity, cyber/physical systems, blockchain, virtual workplace, and digital twins. In fact, virtual models, simulations, and digital twins of factories and plants have been around for nearly a decade, and digital design tools even longer. Virtual training, such as training for airline employees, is also well established. Significant improvements in productivity and efficiency, up to double-digit percentages, have been demonstrated in existing applications.
That said, implementation of Industry 4.0 is still by no means as widespread as was expected a decade ago. It faces several common barriers, including high upfront investment, difficulties in coordinating the required cross-functional transformation, challenges in data security and management, lack of available skills, and limitations imposed by legacy IT systems.
So, what’s new about the Industrial Metaverse? What’s new is a convergence of key technologies leading to a step-change in simulation capabilities (Figure 2).
Up until now, digital twins have been mainly limited to discrete products, components, plants, or factories. Use cases have been mainly targeted at operational and maintenance performance improvement. Further developments in simulation of complex systems, data visualization, and AI, combined with ongoing improvements in connectivity (IoT) and collaboration technologies, supported by increasing computing power, mean digital twins are now becoming possible for multiple connected facilities and systems.
This extends and elevates digital simulation from the level of operational improvements and design aids, towards becoming a key tool for strategic decision-making across complete systems – and ultimately across an entire global industrial enterprise.
Some early examples have already been shown: BMW’s iFactory program involves simulation of potentially all its production facilities to enable a complete production strategy based around the use of digital twins for all production sites.
Perhaps even more impressively, Michelin has applied digital twinning together with complex system modeling to optimize its global sourcing strategy. (See Box 1.)
How best to conceptualize it
Based on this idea of a step-change in simulation capabilities, we can usefully define the Industrial Metaverse as follows:
“A connected whole-system digital twin with functionalities to interact with the real system in its environment, allowing decision-makers to better understand the past and forecast the future”
Figure 3 shows its primary functional and technology building blocks.
At the core is the “whole-system digital twin,” which ultimately could represent a complete end-to-end industrial system, including not just physical assets, but also processes, functions, resources, and organization. It would extend beyond the company boundaries to include relevant players and interactions across the whole company partner ecosystem, both upstream and downstream. It could also eventually include the broader environment within which the company operates. It needs to be constructed as a complex system to enable realistic and dynamic system behaviors to be modeled. Extensive “what-if” simulation functionality is a key part of the twin. Simulations are based on not just past data, but also present and future data.
Four key functions are necessary for the system to operate:
-
Connect: The digital twin is permanently connected to the real-world system through the IoT (for “hot” current data) and ERP systems (for “cold” stored data). Real-time bidirectional connections enable continuous data collection and actuation back onto the system.
-
Compute: The capability to process very large data volumes from the real system, including analytics, complex system modeling, pattern recognition, and simulation, to enable future scenario formulation.
-
Conceive: Visualizing both physical and non-physical data, which may or may not be fully immersive. These visualizations interpret and present complex data in different ways, not only to simulate reality, but also to facilitate understanding and illustrate “what-if” scenarios.
-
Collaborate: Functionality to enable a range of interactions, between internal staff, ecosystem partners, value chain players, customers, and others. Interactions may include commercial transactions as well as everyday co-working.
Figure 3 shows five key technology building blocks that enable this functionality, supported by a sixth computing capability technology block. These technologies, for the most part, exist already. However, further development is needed in all of them to deal with the increasing scale and complexity of data. Increased computing capability itself is a critical enabler for achieving very large, connected digital twin simulations.
Overall, the picture suggests a timescale of five+ years before true connected whole-system digital twins will be feasible, although in the meantime, intermediate steps involving digital twins of increasingly complex systems (such as the Michelin global sourcing example above) are still possible.
Why should companies pursue the Industrial Metaverse?
1. Conventional strategic decision-making is becoming inadequate to meet the combined challenges of complexity, acceleration, cognition, and sustainability
The last few years have seen a mushrooming of complexity in industrial systems – for example, in the last two years alone, the volume of enterprise data has risen by over 40 percent to more than two petabytes, with vastly increasing partner network complexity. At the same time, the pace and unpredictability of change is accelerating. The limitations of human cognition mean making good decisions within these faster-moving, unpredictable systems is difficult. Even more importantly, sustainability imperatives mean end-to-end complex industrial system control is becoming increasingly important, for example, to manage Scope 3 emissions and develop strategies to achieve net-zero growth.
Conventional strategic decision-making is poor at meeting these challenges because it typically relies on oversimplification of complex systems. This means it often misses unexpected system impacts, and can be lagging rather than leading, failing to anticipate and react fast enough to rapid changes. The Industrial Metaverse offers the possibility of allowing companies to take informed C-level decisions based on a dynamic, forward-looking, whole-system approach. This would identify performance improvements and the impacts of change more rapidly and effectively, as well as help deliver on obligations to manage overall impacts and achieve sustainable growth.
2. The business benefits of the Industrial Metaverse, even in the short-term, are significant
As we have noted, even if fully connected, whole-industrial-system digital twins are some years away, organizations can still reap significant benefits from existing applications, many of which overlap with Industry 4.0.
Today’s use cases can be split into four categories:
-
Optimization: e.g., improvements in operation and maintenance, product quality, supply chain, and customer service
-
Training: e.g., operational staff, safety, remote, and product training
-
Technical tools: e.g., design/construction integration, asset inspection/maintenance, and remote troubleshooting
-
Management tools: e.g., virtual meeting, collaboration, transaction, and interaction tools
As digital twins extend beyond discrete plants towards industrial systems, the benefits will surpass productivity and efficiency to include the potentially much greater impacts of better strategic decision-making on overall growth, margin, and shareholder value.
3. The Industrial Metaverse market could accelerate rapidly in a five+ year timeframe
Predicting when technologies will accelerate is always difficult. The sudden explosion of AI, together with advances in complex systems simulation, data visualization, and connectivity, could act as a catalyst. Importantly, unlike with the consumer Metaverse, adoption does not depend on acceptance of immersive virtual environments. Reflecting this key point, Apple’s CEO, Tim Cook, prefers to use the term “spatial computing” rather than “Metaverse.”
The current Industrial Metaverse market size is in the USD100–150 billion range (depending on how you define the scope). Our conservative forecast is that it will grow to around USD400 billion by 2030, although the upside could be more than USD1 trillion, with a CAGR in the 20–30 percent range.
Insights for the executive – What should companies do now?
Companies need to consider their strategy for the Industrial Metaverse in the context of their broader digital transformation journey. Organizations cannot easily “leapfrog” to full Industrial Metaverse implementation unless digitalization is already fairly mature. We suggest four steps:
1. Review digitalization strategy, journey, and position
As a starting point, companies need to have a clear vision and pathway for their overall digitalization journey. Understanding the current position on the digitalization journey helps to determine:
-
What still needs to be done in terms of digitalization basics before embarking on Industrial Metaverse development (such as data availability and infrastructure)?
-
What is a realistic pace of development going forward?
-
What would be a feasible target destination to align with the rest of the digitalization journey?
2. Identify value-adding opportunities and develop a roadmap
Many applications and use cases already exist. In developing the roadmap, companies should consider:
-
What potential applications and use cases would add the greatest value? The initial applications for the Industrial Metaverse are likely to be operational, with an aim to extend towards more strategic applications over time.
-
What is already technically feasible today, versus potentially feasible in coming years? As we have seen, although many feasible opportunities are currently available, large-scale complex industrial system simulations are still some way off.
-
What is the vision and ambition for Industrial Metaverse applications in a five+-year time frame? The scale of ambition may depend upon the scale of digital transformation that companies are already committed to.
In developing the road map, companies should avoid overambitious detailed modeling at the start, as this could stifle early progress. As well as the use cases themselves, the roadmap should consider what new processes are needed to access, update, analyze, interpret, and act upon the required data.
3. Implement pilots, adopt a test-and-learn approach, and manage change proactively
An agile and responsive test-and-learn approach will work best. This means starting small and selecting initial pilot projects that are readily replicable, with relatively short payback times that do not need extensive involvement from external stakeholders. Managing the people impacts of implementation is key, for example, new roles and skills requiring support over an extensive period.
4. Build and align the partner ecosystem, creating a win-win
The major benefits of the Industrial Metaverse are realized through involving not only internal operations, but also the partner ecosystem. This requires sharing of much more data than is traditionally shared between commercial partners, which demands a new mind-set and culture. Mutual benefits should be clearly demonstrated – such as faster customer response, reduced working capital, smoother customer/supplier interfaces, and better management of sustainability impacts. Data management standards and adequate safety and security are also key.
The Industrial Metaverse has tangible business value beyond the hype. Executives should not write it off just yet.
Note
[1] ADL/Blue Shift report The Industrial Metaverse – Making the invisible visible to drive sustainable growth (2023)