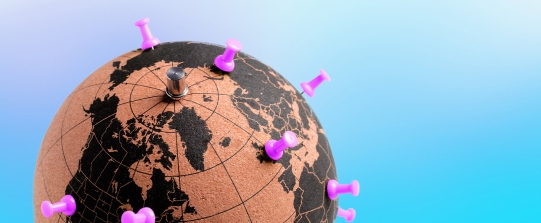
Global supply chains are under scrutiny due to material shortages, rising costs, and ethical demands. Adapting to a changing world is crucial for maintaining robust and responsive supply chains. This Viewpoint highlights the urgency for manufacturing firms to reassess their locations, prioritizing not just cost efficiency but also resilience, adaptability, and responsibility.
THE TIME IS NOW
A series of recent challenges — including material shortages, rising energy costs, new environmental regulations, geopolitical tensions, and intensifying protectionism — have necessitated a reevaluation of the current global supply chain model. Evolving consumer demands for transparency around product origin, environmental impact, and labor practices have exposed vulnerabilities in extensive supply networks and impacted profitability and recovery capabilities. Consequently, manufacturing location decisions are now more critical than ever and extend beyond cost savings and efficiency to encompass a company’s adaptability and responsibility in a complex global market. In the face of this upheaval, manufacturing firms must reconsider their geographic footprint. In this Viewpoint, we present a strategic framework to guide a thorough reevaluation, focusing on how manufacturing location decisions affect a company’s cost efficiency, resilience, adaptability, and ethical integrity.
The post-pandemic recovery and ongoing geopolitical disruptions have underscored the need for a critical reassessment of supply chains. In 2024, key challenges include the weakest global economic growth in decades, rising inflation and energy costs, conflicts in Europe and the Middle East, tensions between the US and China, and global banking instabilities. And, as companies aspire to lessen their environmental impact and achieve net zero, they face the additional task of addressing the emissions generated by long supply chains.
Disruptions from pandemic peaks have eased, but executives still report significantly higher levels than pre-pandemic. Significantly, this led to a 128% increase in mentions of “reshoring” in S&P 500 earnings calls in early 2023 compared to the same quarter in 2022, according to analysis from Bank of America.
This Viewpoint highlights three urgent reasons to reassess manufacturing footprints (see Figure 1):
-
Understand actual cost of a globalized network.
-
Ensure supply chain resilience and risk mitigation.
-
Adapt to customer sentiment.
Moreover, emerging regulations are contributing to existing pressure on global supply chains:
-
The US Inflation Reduction Act (IRA) and Infrastructure Investment and Jobs Act (IIJA) are catalyzing US domestic manufacturing, especially in the clean energy and electric vehicle (EV) sectors. Both offer tax credits and grants, with the IRA’s Section 45X providing tradable tax credits to offset the higher cost of US-made components. These incentives led to a surge in US manufacturing investments, with new domestic EV and battery factory announcements reaching US $210 billion by early 2023, surpassing China. These programs aim to balance higher US production costs with financial incentives to encourage reshoring in strategic industries.
-
To protect its national security, China announced a new export license policy for graphite in October 2023. China controls 67% of the global supply of graphite and refines over 90% for EV battery anodes, pushing automakers like Tesla and Mercedes to seek alternative sources.
-
The EU’s Carbon Border Adjustment Mechanism (CBAM) is a tariff that requires certain industries to record emissions for imported goods. Its first phase took effect in October 2023; carbon permits will be required by January 2026. This legislation is prompting non-EU high-emission producers to seek domestic production and eco-friendly suppliers.
Understanding actual cost of globalized networks
Reevaluating the total cost of ownership for global supply chains requires a comprehensive analysis that goes beyond direct expenses to include complex indirect costs and sourcing details. Complexity comes at a price; saving in one domain, such as labor costs, can lead to higher expenses in another. In fact, a 2021 report from the Economist Intelligence Unit (EIU) revealed that supply chain disruptions experienced during the pandemic resulted in costs averaging 6%-10% of annual revenues and did not account for additional expenses incurred to repair brand reputation and respond to customer complaints. As a result, numerous companies have strategically opted to regionalize and simplify their supply chains to mitigate the impact of future disruptions.
Reducing labor costs has traditionally been the primary motivation for outsourcing. However, the advantages of sourcing from low-cost countries are diminishing for two reasons:
-
Rising wages in developing countries. In 2022, real wages in China increased by 2.6 times compared to their 2008 levels, whereas in the US, wages have increased by approximately 1.1 times during the same period (see Figure 2).
-
Opportunities for automation. These are addressing and alleviating one of the key challenges of nearshoring — labor availability. At the same time, the growing shift toward production electrification is boosting the demand for accessible, affordable, and sustainable energy, which in turn influences decisions on manufacturing locations. These factors are driven by business necessities and further supported by global policies.
Ensuring supply chain resilience & risk mitigation
The COVID-19 pandemic, the Suez Canal blockage, and the semiconductor chip shortage revealed the global supply chain’s fragility. These disruptions truly showed the interconnectivity of global trade: when products get stuck, revenue is lost, customer relationships are damaged, and resolution costs increase. It is a lose-lose situation.
The EIU survey also highlighted a significant shift in post-pandemic executive priorities, with 60% emphasizing resilience and risk mitigation over speed and efficiency. This trend has persisted, as evidenced by a 2023 UBS survey, where 70% of 1,600 US executives indicated plans to relocate their supply chains closer to customers to achieve greater risk mitigation (see Figure 3).
Recent industry announcements provide concrete examples of this trend:
-
Novo Nordisk. In 2023, the Denmark-based company began allocating $5.9 billion (DKK 42 billion) to enhance manufacturing by expanding its Kalundborg facilities and planning a new site in Funen for chronic disease products.
-
Mini Cooper. Production of the first Mini Cooper made entirely in Germany began in Leipzig in November 2023, marking a new manufacturing milestone for the BMW Group brand.
-
Intel. The company invested $20 billion to build two new chip factories in Chandler, Arizona, USA. The state’s largest private investment aims at boosting US semiconductor production and is projected to create over 3,000 jobs by the end of 2024.
By decreasing geographical distances and complexities in the supply chain, nearshoring can significantly enhance operational resilience and mitigate risks. It facilitates quicker response times, improves supply chain visibility, and strengthens control over production processes while reducing inventory and working capital. This approach not only supports faster adaptation to market changes but also fosters stronger, more reliable customer relationships — a crucial advantage in today’s volatile global market.
Adapting to customer sentiment
Today’s consumers are particularly focused on ethical and sustainable practices and push companies to move beyond efficiency to deliver experiences aligned with their values. Gen Z, poised to become the largest consumer group by 2030, is at the forefront of this shift. A 2023 report from the Swedish Trade Federation found that 70% of Gen Z consumers avoid brands that do not match their ethical principles, and 73% are loyal to brands that do. Authenticity matters to this demographic, which is wary of greenwashing.
The shift toward supporting companies based on their ethical choices extends beyond Gen Z, as concerns about global supply chain issues — like higher emissions and labor concerns — are driving a turn toward domestically produced goods. The “Made in America Report” from Morning Consult Pro in June 2023 showed that 65% of US consumers prefer domestic products, with 48% ready to pay more, reflecting rising sentiment and environmental, social, and governance (ESG) considerations (see Figure 4). This evolving landscape requires businesses to rethink their supply chains to balance cost and efficiency with ethical, sustainable practices and assured quality.
GETTING STARTED
The process of reviewing the manufacturing footprint is complex and multifaceted and requires careful planning, deep analysis, and strategic thinking. Figure 5 illustrates the main initial steps to undertaking this review:
-
Map current state. This step involves analyzing existing facilities, locations, and operations and is essential to reevaluating manufacturing footprints. Key aspects to examine include cost structure, production capacity, outgoing logistics, inventory and lead times, competitive landscape, and growth opportunities to pinpoint improvement areas.
-
Define future ambitions. Aligning the supply chain with the company’s vision, values, brand, and reputation is crucial. This includes adhering to sustainability policies and meeting ESG demands. Furthermore, efficiency in the supply chain results in resourceful operations, minimizing costs while maximizing speed and emphasizing proximity to demand. As supply chains become more local, improving or maintaining productivity levels is vital to remain competitive.
-
Plan for gradual improvement. Ambidexterity is important for long-term strategic growth and optimization and can be achieved by identifying quick wins for immediate improvements and concurrently developing future roadmaps. This balanced approach ensures immediate positive impacts and sustained progress toward overarching goals.
-
Develop business case and roadmap. This final stage confirms that the updated manufacturing footprint aligns with the company’s overall business objectives. It includes integrating strategic alignment, risk management, sustainability, and efficiency. Performing a cost-benefit analysis, especially in scenarios like reshoring, is critical for balancing immediate benefits with long-term value, while also keeping in step with market dynamics and meeting regulatory requirements.
Conclusion
THE TRIFECTA PUSH FOR SUPPLY CHAINS
In the wake of the pandemic, global businesses are grappling with risks and disruptions in their complex manufacturing networks, which have been intensified by current geopolitical conditions. Three factors have escalated the need to strengthen the resilience and future readiness of supply chains:
-
Awareness of high costs and vulnerabilities of globalized networks in the post-pandemic era
-
The pressing need to push toward domestic and regional production to enhance control and diminish risks
-
Consumer demand for transparency and ethical practices, fostered by a preference for domestically produced, sustainable goods
To achieve a more adaptable, ethical, and efficient supply chain, we advise executives to reassess their manufacturing strategies and focus on cost, resilience, and consumer trends.